Teil 16 der Umbau-Story:
Winter-Pause oder Kleinste Schritte (11./12.2021 und 01.-04.2022):
Ich wusste das wird zäh, aber so zäh ...
Hatte ich schon erwähnt, das ich Blecharbeiten hasse? Das war auch der Grund warum ich vor über 30 Jahren meinen schönen VOLVO Amazon P121 abgestoßen habe. Ich wäre aus dem Blechnern sonst nie wieder herausgekommen!
Nach langem fummeln und kleine Schritte machen bin ich nun endlich mit der Sitzbankplatte fertig geworden. Zusätzlich motiviert hat mich auch noch die Nachricht, dass mein TÜV-Prüfer, bei dem ich bisher alles habe prüfen lassen, dieses Jahr noch in den wohlverdienten Ruhestand geht. D.h. wenn er es noch prüfen soll - Wamanos Muchacho!
Aber erstmal Klein-Klein:
Wie im vorhergehenden Bericht erwähnt, wollte ich die grob in Form gebrachte Sitzbankplatte verlängern, damit sie mit dem geschraubten Loop abschließt. Dazu habe ich die Form vom Rahmen auch eine Pappschablone übernommen und auf 1,5 mm Stahlblech (dummerweise habe ich verzinktes Blech erwischt) übertragen, das dann zurechtgeschnitten und gefeilt wurde. Wie bördele ich das ganze aber um? Es soll schließlich der rund 2 cm tiefe Rand der Original-Sitzbank fortgeführt werden um den dann der Bezug herumgeschlagen und gespannt werden soll!
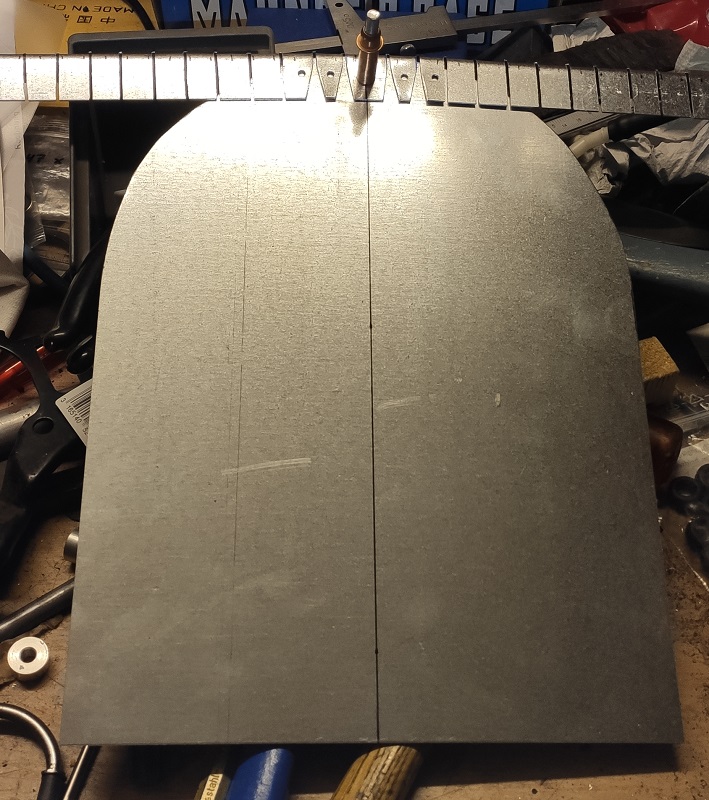
Grundplatte
Nach ein bischen Nachdenken wurde ein Blechstreifen mit 1 mm Dicke (dummerweise wieder verzinkt) der Länge nach um 90° umgebogen und am oberen Flansch in 1,5 cm-Abständen mit der Blechschere Dreiecke herausgeschnitten. Damit konnte ich den Streifen dann an die Form der Grundplattenverlängerung anpassen.
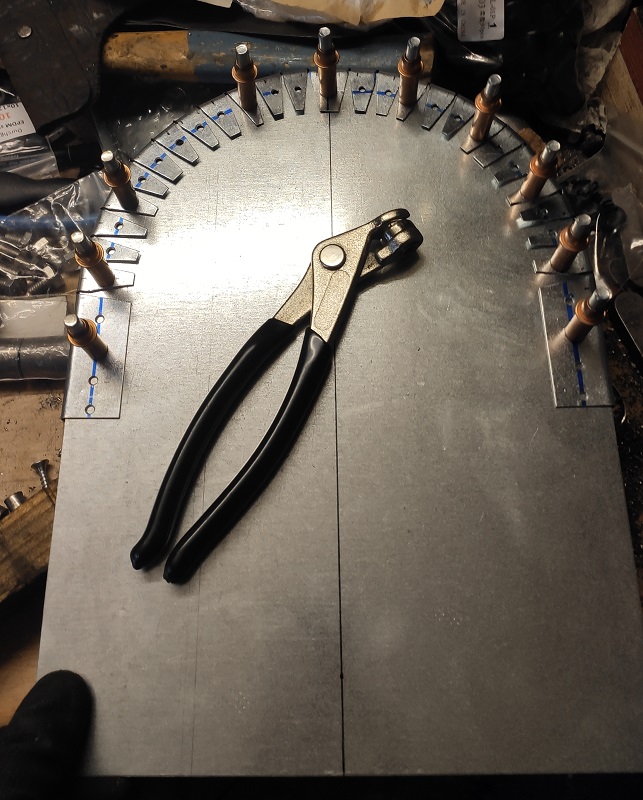
Randstreifen
Da man das natürlich nicht sofort festschweißen kann (mir würde dazu auch das Schweißgerät fehlen), musste ich das Band irgendwie provisorisch und lösbar mit der Grundplatte verbinden. Mein Nachbar gab mir hier dann eine geniale Anregung: Er restauriert gerade einen Synchro-Bully und muss dazu umfangreiche Karosseriearbeiten machen (ich würde das zwar nie machen, aber er hat meine uneingeschränkte Bewunderung dafür!). Um die Kotflügel und die anderen Karosserieteile zu fixieren, benutzt er Spannstifte, die ich vorher noch nie gesehen habe, die aber dafür absolut genial sind: Cleco-Pins! Er benutzt 3mm Pins (müsste 1/8" sein). Um diese zu verwenden, bohrt man durch beide Bleche ein 3mm Loch, setzt den Pin mit der Zange ein und schon sind die beiden Bleche zueinander fixiert - klasse! Da ausleihen zu langwierig war (er brachte seine schließlich selber) habe ich mir kurzerhand einen kleinen Satz gekauft. Zum Glück ist das keine hohe Investition, also her damit!
Nachdem die Kante dran war wurde die Grundplatte an die Form des Hecks der XS angepasst. Dazu musste ich die Platte innen ausschneiden und biegen. Hier zahlten sich die Cleco-Pins aus. Man konnte alles zerlegen und dann punktgenau wieder zusammensetzen! Für die noch offenen Bereiche zwischen der Grundplattenverlängerung und der Sitzbankplatte wurden Abdeckbleche zurechtgeschnitten und gebogen. Dafür verwendete ich 0,7 mm Schwarzblech, das sich fast so einfach wie Karton mit der Blechschere bearbeiten lässt. Um die Form zu ermitteln wurden die Öffnungen mit einem Karton abgedeckt und dieser zurechtgeschnitten, dann wurde die Form dieser Vorlage auf das Blech übertragen und dann das Reparatur-/Abdeckblech hergestellt. Das ging doch recht flott. Trotzdem hat sich die Summe der Arbeiten den ganzen Winter hingezogen, da, wie schon erwähnt, meine Motivation für Blecharbeiten eher gering und die Werkstatt kalt waren.
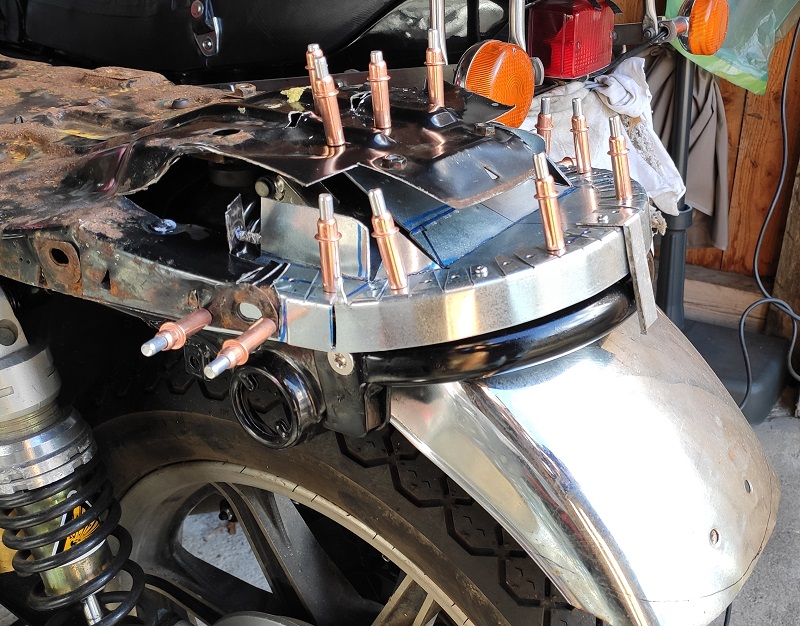
Heckbürzel-Rohbau
Aber jetzt wollte ich endlich damit fertig werden! Als alle Bleche vorbereitet waren, demontierte ich alle Gelenke und Gummipuffer von der originalen Sitzbankplatte und mein Nachbar hat sie dann zeitnah sandgestrahlt, alls er gerade dabei war den Bully-Unterboden zu entrosten. In 3 Minuten war das erledigt und ein paar neue Löcher im alten Blech haben mich angelächelt, nach dem der Rost weggeblasen war! Grrrrrr!
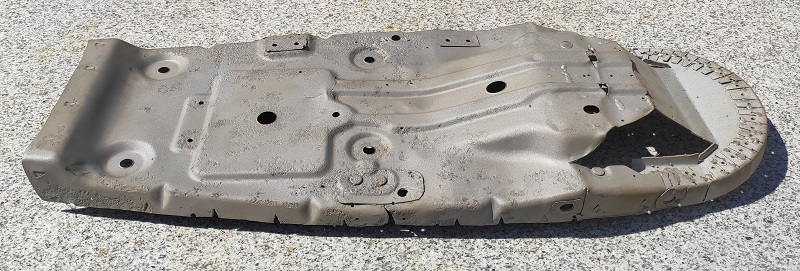
sandgestrahlte Grundplatte
Um das blanke Blech nach dem Sandstrahlen zu schützen, wurde die Sitzbankplatte mit Schweißprimer lackiert. Dann ging es endlich ans Schweißen! Dazu durfte ich eine der Schutzgasschweißanlagen meines Brötchengebers in der Instandsetzungsabteilung nutzen. Ein Kollege hat mich in die Maschine eingewiesen und mit mir zusammen ein paar Punkte geschweißt, dann traute ich mir zu den Rest selber zu machen. In einer mehrstündigen Session wurden dann alle Bleche festgeschweißt und die Rostlöcher ebenfalls mit Blechen verschlossen und stabilisiert. Zum Ende und einer letzten Anpassung wurde dann der Anschluss am Tank um 2 cm verschmälert und mit Schweißpunkten fixiert. Jetzt sieht auch dieser Bereich gefälliger aus!
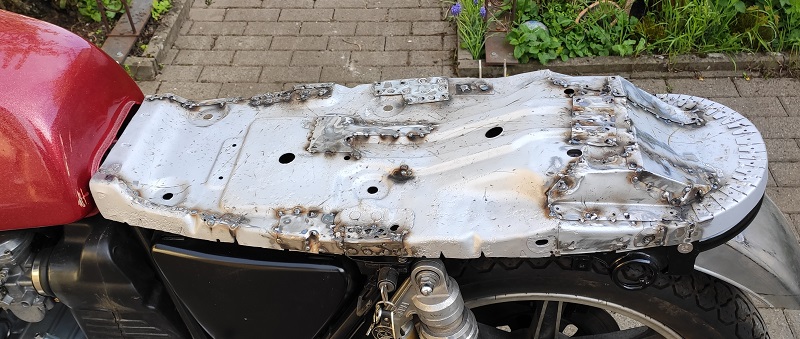
Probemontage der geschweißten Platte
Nach einer Probemontage (alles hat gepasst und die Platte lies sich aufklappen) kam die umgearbeitete Platte wieder runter und wird jetzt mit Hammerit-Lack schwarz gestrichen. Als nächstes kommt dann der Aufbau der Sitzbank mit Schaumstoff dran!
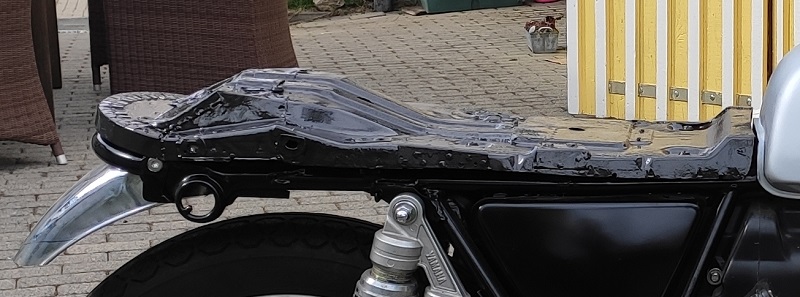
Lackierte Sitzbankplatte
Parallel zu den Arbeiten an der Sitzbankgrundplatte wurden im letzten Halbjahr noch weitere kleinere Arbeiten ausgeführt.
Die Instrumentenkonsole war noch herzustellen. Nach langen Überlegungen und auch Feedback hier im Threat entschloss ich mich beide "Uhren" der XS in Originalgröße zu verwenden. Aber das riesige Kontrolllichtpanel der XS passt nicht zu meinen Vorstellungen! Erst liebäugelte ich mit der Konsole der XS650, aber eigentlich wollte ich auch eine Richtungsanzeige der Blinkkontrolllichter. Bei weiterer Recherche fand ich dann die Konsole der XS1100S, die alles anzeigte was ich wollte, aber erheblich dezenter und gefälliger in der Form ist. Aus meinen XS1100-Projekt hatte ich natürlich noch Kontakte und Quellen und habe diese dann angefragt. Werner Maier von der XS1100IG hatte das gewünschte im Fundus, wenn auch nicht ganz unbeschädigt. Aber für den Anfang reichte es. Kurz darauf kam alles bei mir an und ich hielt die Konsole an meine 850er. Es passte! Aber die Konsole war zu weit weg von der Brücke, da normalerweise noch das Zündschloss dazwischen montiert ist. Das Zündschloss wollte ich aber unter den Tank bauen (so wie früher bei den Engländern und den ersten Japanern, z. B. meiner Fahrschulmaschine, der CB200), also konnte ich die Konsole wohl etwas kürzen um die "Uhren" näher an die Gabelbrücke rücken zu lassen. Nachdem Maß genommen wurde, kam das Schlosser-Universal-Werkzeug No. 1 zum Einsatz: Meine Handbügelsäge. Nach ein paar beherzten Schüben waren die Überflüssigen Laschen gekürzt und dann die Bohrungen zum Verschrauben gesetzt. Mit ein paar Feilenstrichen wurden noch keine Anpassungen gemacht und alles sah (in meinen Augen)prächtig aus!
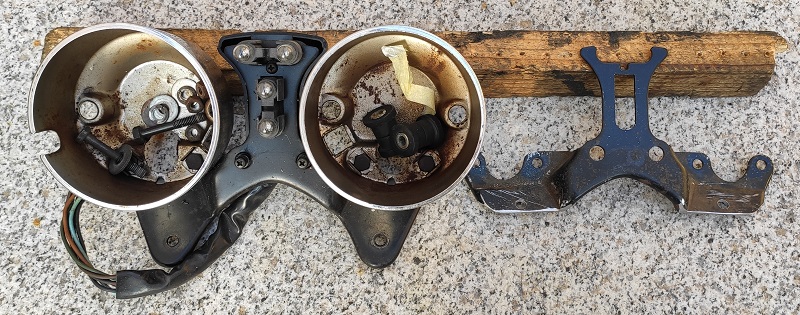
Instrumentenkonsole - links Original - rechts gekürzt
Um das ganze auch optisch aufzuwerten wurde der Halter im Anschluss sandgestrahlt und schwarz pulverbeschichtet. Das Ganze machte dann einen extrem profimäßigen Eindruck! Die Kontrolllichtbox wurde dann montiert und die Konsole oben am Lampenhalteradapter der XS verschraubt, Becher montiert und "Uhren" eingesetzt. Das sieht prima aus! Ich bin zufrieden!
Auch die Fahrerfußrasten wurden gegen gefälligere Exemplare ersetzt. Die Originalen Rasten sehen schon arg klobig aus. Beim Stöbern im KEDO-Katalog bin ich dann auf Alu-Rasten für die XT600E/K gestoßen, "KEDO Street Pegs" wie diese im Katalog heißen. Im Vertrauen auf das Yamaha-Baukastensystem habe ich ein Paar bestellt. Die passten auch, konnten aber nicht hochklappen, da diese an der Montageseite nur an der Oberseite abgerundet sind. Was tun, zurückschicken oder anpassen?
Aber was mache ich hier? Customizing? Also wurde angepasst! Mit der Feile war der notwendige Radius schnell an beide Rasten dran und nach ein bisschen Probieren und Nacharbeit hat das Klappen funktioniert. Leider war bei den KEDO-Rasten kein Bolzen dabei (bei der XT kann er wohl das Original wieder verwendet werden), also wurde in der Bucht ein Paar Fußrastenbolzen geordert. Damit konnten die Rasten dann sehr einfach montiert werden. Wieder ein Schritt gemacht! Als Beifahrerfußrasten wurde ein Satz Rasten der FJ 1200 verbaut. Die passen optisch nicht ganz optimal, da diese einen Stahlkörper haben, aber für die FJ gab es die auch welche aus Aluminium, da muss man einfach den Markt beobachten und zuschlagen, wenn diese angeboten werden!
Außerdem erfolgte eine Probemontage der verschiedenen Scheinwerferoptionen. Zum einen der 22 cm durchmessende "Flak"-Scheinwerfer, der auch Original an die XS850 gehört oder der kleinere "Normalo"-Scheinwerfer". Da ich den Lampenträger der SR500 verwendet habe, kann ich beides problemlos ausprobieren, da die Grundhalteplatte immer gleich ist und nur die Lampenhalterarme getauscht werden müssen. So, hier das Ergebnis mal optisch:
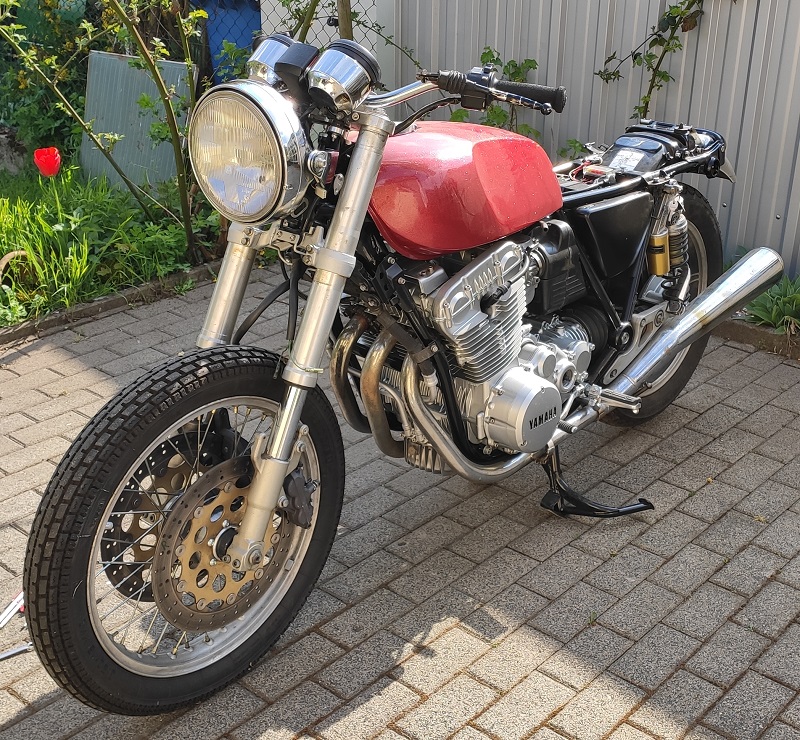
"Flak"-Scheinwerfer (220 mm)
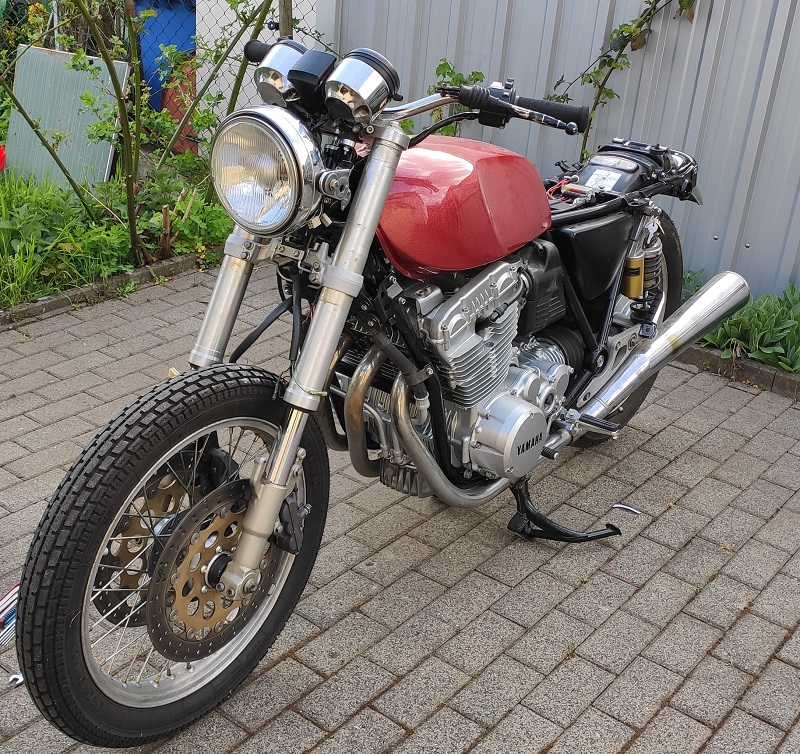
"Normalo"-Scheinwerfer (200 mm)
Vorteil der "Normalo"-Version ist, das es hierfür viele Alternativen, wie Klarglas-Scheinwerfer und ähnlichens gibt. Der "Flak"-Scheinwerfer aber typisch ist für die Yamahas dieser Epoche! Ich tendiere, auch nach dem Vergleich, stark zum "Flak"-Scheinwerfer!
Dann hat mich aber doch der Elan übermannt! Um ein wenig eine Vorstellung davon zu bekommen, wie der Tank in Alufarben auf der XS wirkt schnappte ich mir kurzerhand Zink-Alu-Spray und habe den Tank damit eingenebelt. Am nächsten Tag wurde die fertig lackierte Grundplatte und der Alu-farbene Tank montiert, kurzerhand die kurze Auspuffanlage angebaut und provisorische Halter dafür hergestellt. Zum krönenden Abschluss wurde der von KEDO gekaufte Frontfender aufs Vorderrad gelegt und ein Haufen Bilder gemacht. Jetzt sieht mein Umbau endlich so aus, wie er mir die ganze Zeit im Kopf herumgeschwebt ist!
Hier mal die Bilderserie:
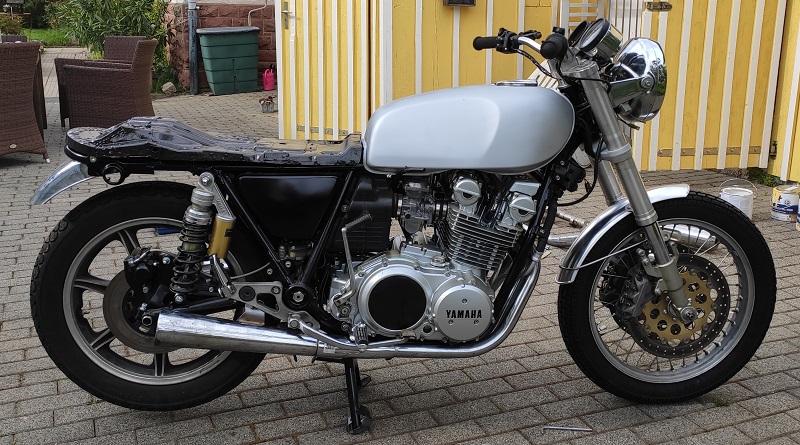
Gesamtansicht von rechts
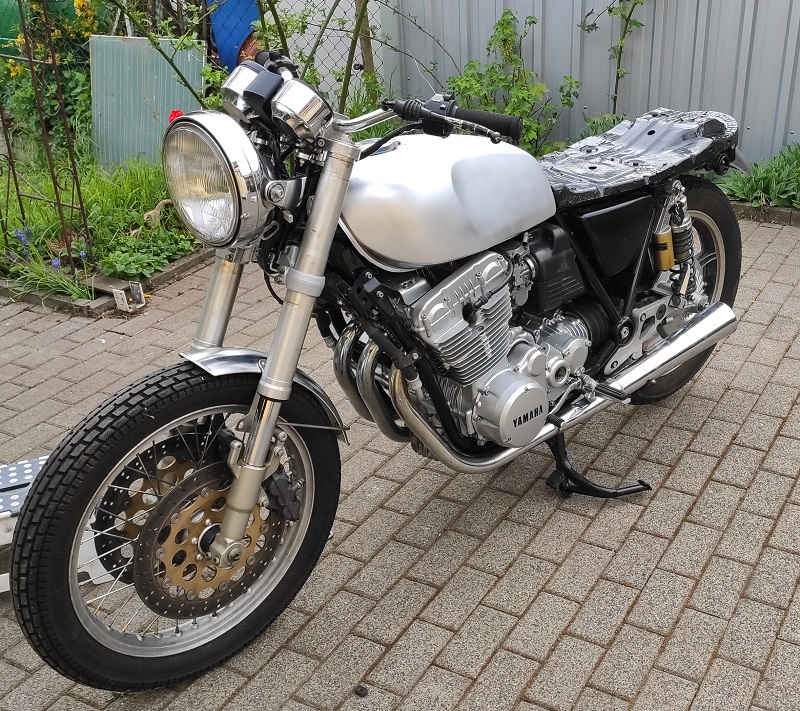
Ansicht von vorne links - Natürlich fehlen noch ein Haufen Kleinteile! Aber als erste Ansicht gut!
Was als nächstes kommt sind der Aufbau der Sitzbank und der Frontfender ist zu fest anzubringen (auch hier ist ein neuer Halter zu bauen). Außerdem muss ich mich für eine Lenkerbauart entscheiden. Ich mach dann mal ein paar Bilder der Lenkeralternativen, mal sehen, was ihr meint! Wenn der "endgültige" Lenker dran ist muss auch die Bremse angeschlossen werden. Was auch noch ansteht ist, neben der Komplettierung der Beleuchtungs- und Signalanlage, das Neu-Einspeichen der Drahtspeichenräder mit den passenden Felgen und Tragfähigkeitsgutachten. Es gibt also noch einiges zu tun und nur noch wenig Zeit!